Clyde Companies Uses HCSS to Allocate Fuel
“Going from a paper process to an automated, streamlined process and being able to track with greater accuracy and with more record-keeping tools — our accuracy went through the roof. Our costs were allocated correctly and tracked directly to the equipment and jobs, and it just became a really fluid process for us.”
– Darren Paulson, Director of Business Systems | Clyde Companies
When Clyde Companies, Inc., the parent company for W.W. Clyde & Co., Sunroc Corporation, and Geneva Rock Products, purchased FuelerPlus nearly a decade ago, the company was looking for a way to track all their dispensed fuels to the trucks and equipment on their job sites.
Previously, the mobile oilers and fuelers had a paper log on a clipboard or in a metal container. They would track fuel and fluid dispensed to each piece of equipment on the job, and that paper would eventually make its way back to the office to be entered into the accounting system.
While they were getting accurate equipment usage data from the field, reported fuel costs rarely seemed to match up with what the mobile oilers were reporting, leaving them with a ton of unallocated fuel.
The Clyde Companies turned to HCSS FuelerPlus, a mobile software that allows your fuelers to report more accurate fuel and fluid data in the field and send it directly to your shop and accounting departments to ensure your costs line up.
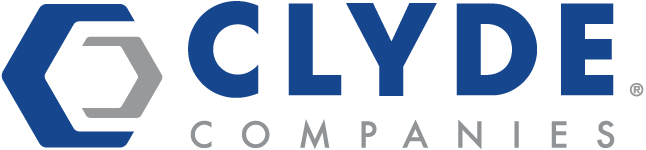
WHO:Clyde Companies, Inc.
WHERE:Orem, Utah
INDUSTRY:Civil Construction, Residential Construction, Commercial Construction
SOLUTIONS:FuelerPlus
They started using FuelerPlus first on a drill-and-blast excavation project on a large mine and saw such a drastic difference in reporting accuracy that they implemented it across all three companies.
Project Manager Taylor Clyde, who was the Project Engineer for the mine job, said they were charged for millions of dollars of fuel for the multi-year, equipment intensive project.
“With our mobile lube engineers using FuelerPlus, it was allocated so correctly that the variance from purchased fuel to tracked dispenses was well below 1 percent,” he said.
Paulson said the ability to work connected to WiFi or cellular service, or to work unconnected on remote job sites and sync data to the office later is another huge bonus for FuelerPlus.
The oilers bring in all their jobs and the dispatched equipment before they leave the shop in the morning, perform their work in the field and record fuel dispensed and meter readings to FuelerPlus, and then send that data directly back to the office when they reconnect.
“Our number of errors has gone down because now there’s a single source where we enter the info into the tablet,” Paulson said. “It removes the entire process of manually entering the numbers and waiting for the results, so we have that data really at the end of the shift.”
“Every day, we know exactly how much fuel we’ve used and the exact meter readings on those pieces of equipment. We use that for our standard maintenance and our records to keep those accurate and up to date.”
– Taylor Clyde, Project Manager | Clyde Companies
The Clyde Companies have also integrated FuelerPlus with HCSS Dispatcher. Once equipment is dispatched to a job using the software, the mobile oiler has a list of equipment that will be on the job site, including the list of services required for that equipment, all on their mobile device.
“It’s been really nice to help facilitate them knowing, ‘Here’s what I need to service,’” Paulson said. “It’s all right here in one system. They get to the job, start at the top, work down all the pieces of equipment, and they have a nice little checklist of everything they need to do, all in one place.”
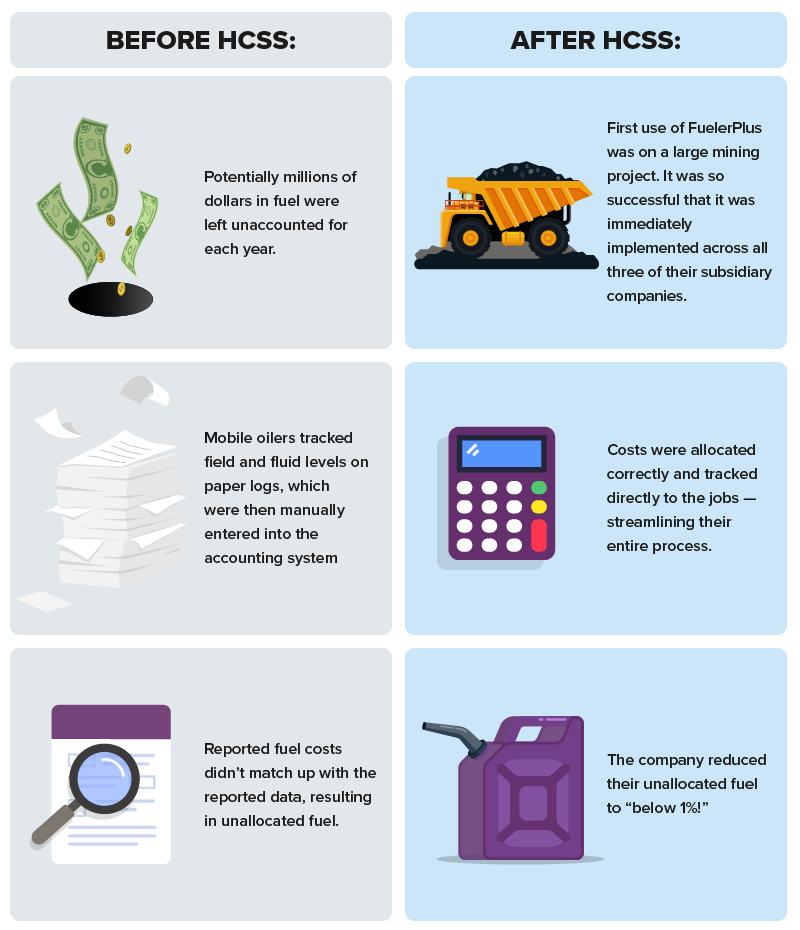