People and fleet equipment are the largest investments that construction companies make. When injuries and accidents happen to either, you lose productivity time, administration costs, and can gain a negative reputation for on-the-job issues. HCSS Safety helps construction companies protect their people, equipment, and productivity by enabling Foremen in the field to communicate in seconds. Instead of waiting days for paper time cards or notes to make it into the office, Foremen can instantly log important safety information - like inspections on each piece of equipment used that day.
When used in conjunction with Equipment360, HCSS Safety is even more powerful with inspections being sent straight to the shop. It’s never been easier to connect the field, shop, and office so you can build faster than ever.
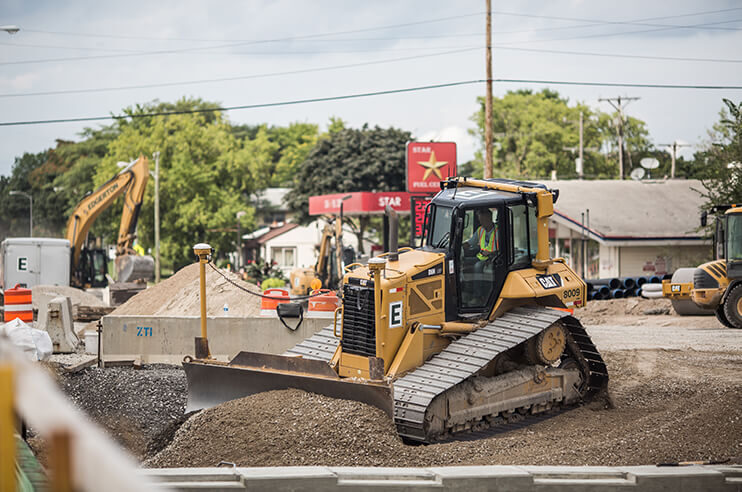
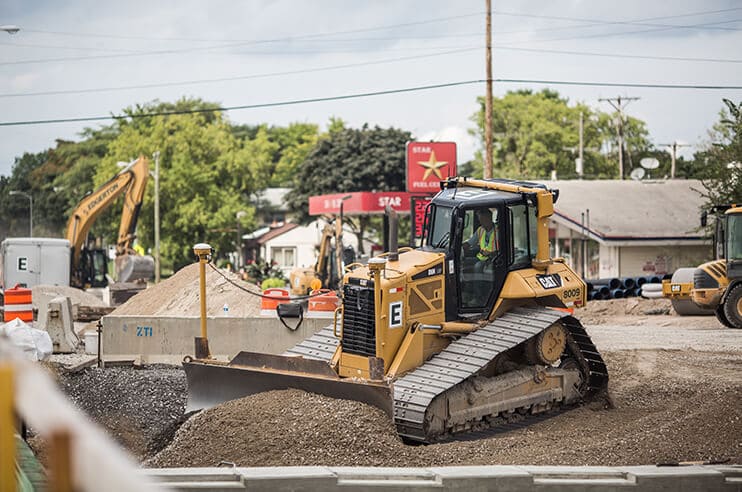
So how does it all work?
HCSS Safety lowers the risk of incidents in the field with tools that help develop a culture of safety in your crews. Foremen and Safety Managers are always prepared for the unexpected with hundreds of toolbox talks, comprehensive inspection reports, crew skill tracking, and safety trend reports that recommend if any specific training topics are needed. Everything logged in Safety is saved so it only takes minutes instead of days to make quick reports for external compliance or internal reporting. Whether it’s faulty equipment or obvious defects, downtime can hurt the whole company
When equipment fails due to an ignored mistake, you risk your operation being shut down. In HCSS Safety, Project Managers are always up to date since they receive safety information once it’s submitted and can help take action to protect your people and equipment.
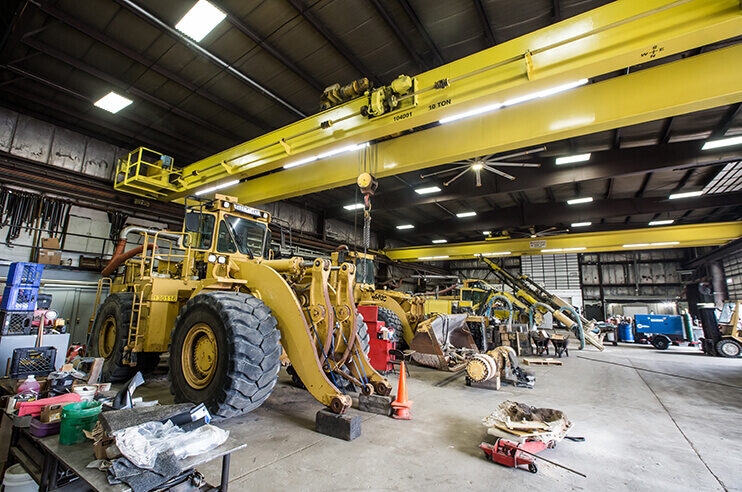
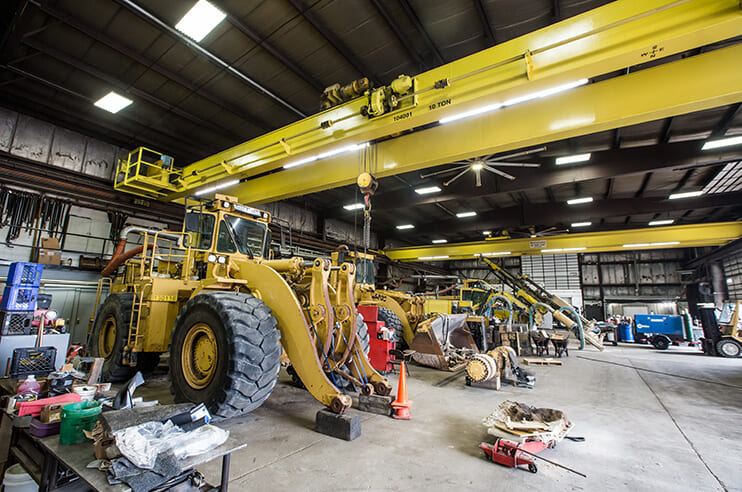
Equipment360 and HCSS Safety Integration
Integrating Equipment360 and HCSS Safety speeds up the communication from the field to the shop. As inspections are being performed in Safety, any failed items can be sent as an alert directly to the Equipment360 Manager's dashboard. From there, fleet managers can add the alert to a work order, backlog the work, or dismiss the alert. Back in HCSS Safety, the status of the alert or work order is visible and can be viewed in the inspection form where the issue was reported. Without this cross-team visibility, safety managers can miss items to check, paper reports would get lost in transit, and there would be no way to confirm any urgent repairs.
So what comes out of more integrated software?
Transparency on both sides. Fleet managers, project managers, and shop owners can open conversations on how to ensure safety and make decisions on future usage of key equipment. Holding safety meetings with your team gives the chance to discuss a variety of concerns. How are your operators handling equipment? Are there any new issues that need to be reported? What are ways to reduce downtime? Having HCSS Safety and Equipment360 work together bridges communication between the field and the shop, helping your team catch potential failures before they happen and prevent equipment downtime.
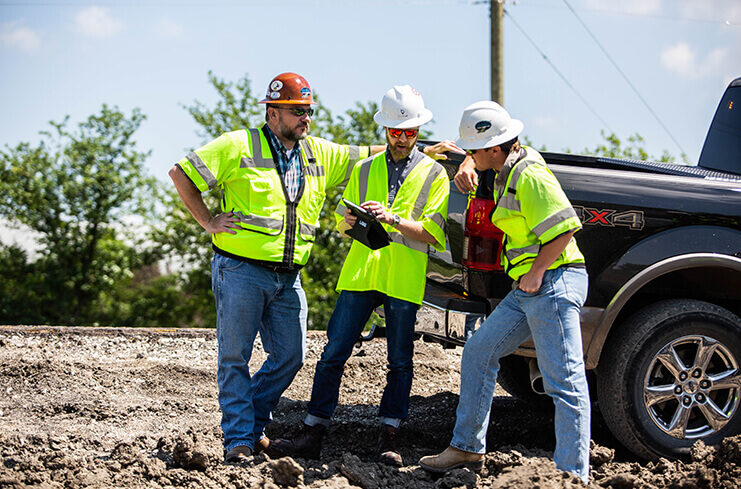
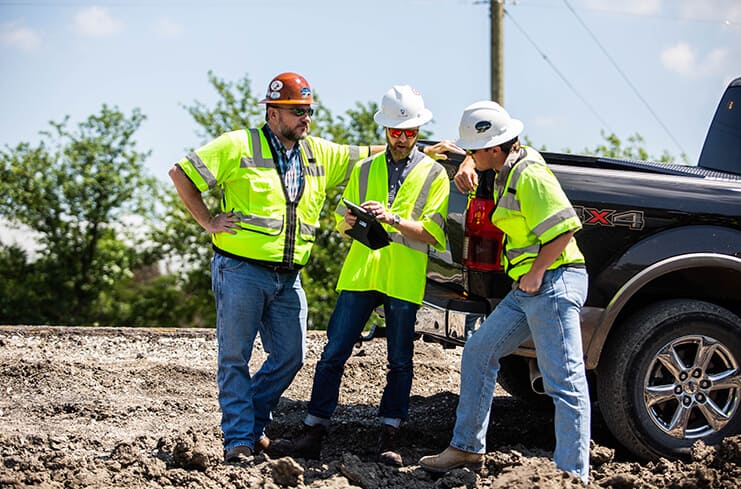
Equipment360 does all the heavy lifting when it comes to prioritizing work and tracking the history of each machine. Work orders can be created and assigned in just 2 clicks so there are less paperwork delays and mechanics are always focused on the highest priority tasks. Problems can be identified and fixed faster when equipment information (like the latest inspections, maintenance records, and work history) is available both on mobile devices in the field and on desktop computers back in the shop.
Both your equipment and your people can safely stay productive when you use HCSS Safety and Equipment 360.