Starting back in 1956, McInnis Construction has gone through multiple iterations to get where the company is today. Following a career with the Alabama DOT as a state bridge construction engineer, current HSE Manager, Scott Overby, joined the McInnis team in 2018.
“They hired me on to set up and develop a safety training and policy procedure program,” Overby says. “There was a consciousness of safety, but it wasn't a priority. Since 2018, every year it has done nothing but improve.”
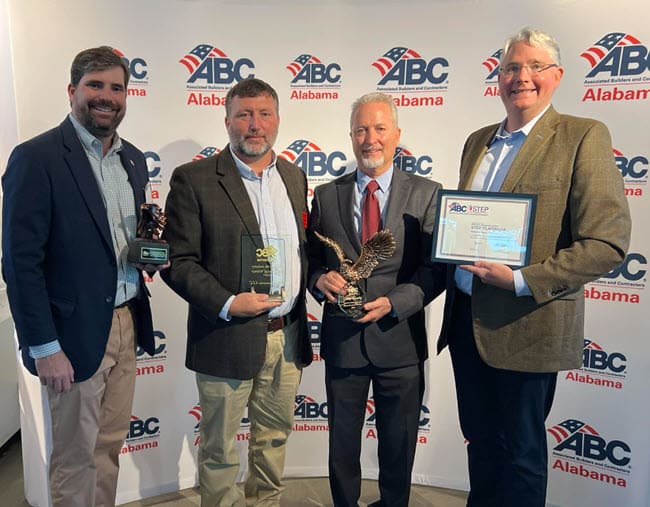
Overby recalls a time he was told by Jim Goss, Senior Safety Consultant at HCSS, that it takes five years to change a safety culture. Now that it’s almost six years into their safety journey, Overby can attest to how the culture at McInnis has definitely changed.
Start Your Day with a JHA
Since safety is now of vital importance for McInnis, not just in writing or as a slogan, the company opens its meetings every day with a prayer for two things: safety and production. “Putting that emphasis on it makes it a high priority in everybody's mind, and the slang for this year was, ‘Start your day with a JHA!’” Overby says.
Always making room for growth, their observation program on jobsites has been developed significantly and continues to evolve for the better. The owners of McInnis made a bold move in recent months to help improve their safety culture by incentivizing safety.
A common hangup construction companies have with handing out bonuses for excellent safety streaks is the possibility of preventing someone from reporting an incident for fear of losing additional income. This concern has been pre-calculated by McInnis, and the team has taken action to ensure that doesn’t happen.
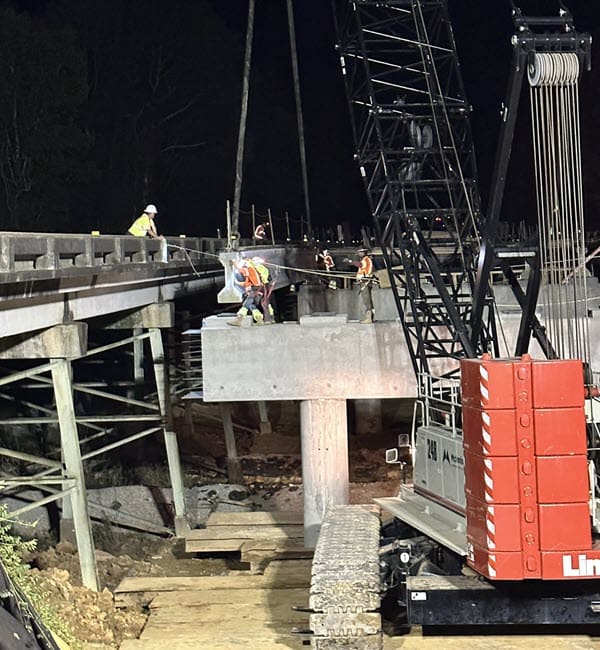
“Every week, I document through HCSS,” Overby comments. “I run that safety metrics report, and I can see who’s doing their meetings, who’s doing their JHAs, who’s doing their near misses, who’s doing their observations, and even the safety inspections on the equipment. That’s sent back out on Monday, in the form of what I call a stoplight-golight report.”
For this report, items are highlighted in one of three colors.
- Yellow means you need to improve.
- Red means you made a mistake.
- Green means you're on track.
Every quarter, if workers have filled out 100% across the board – not being penalized for tracking mistakes you can learn from – they will receive an extra $200 on top of their pay, and then their name goes in a drawing to receive up to an additional $1,000. At the end of the year, whoever is named the Safety Professional of the Year at their annual Christmas party gets $2,000 cash.
Falls: the Biggest Threat on Construction Sites
Everyone in the construction industry knows the leading cause of injuries and deaths come from workers falling on jobsites. According to Overby, there's a lack of training that goes on with many companies, especially by them not placing a special emphasis on fall protection, in particular.
“They just buy the equipment, maybe watch a video and do OJT [on the job training] and they think people are protected,” Overby laments. “But that is not the case.”
Even at McInnis, Overby will admit they started off a little rough, not emphasizing leading edge requirements for SRLs (self-retracting lifelines) as well as they should have early on.
“The thing that changed us was starting a new employee orientation,” Overby adds. “You will be trained in fall protection, set up with your harness, and set up with your lanyard. You’ll have your trauma safety step device connected, and you’ll get all the classroom training. But the real learning comes in the field.”
For OJT, McInnis always has an experienced employee working with an inexperienced employee. When employees first come to work for McInnis, they wear a green hard hat for their first year.
“The green hard hat is an indicator to every employee out on our jobsite,” says Overby. “We have to pay special attention to the green hat employee because we assume they know nothing, and we will teach them everything.”
Above all else, Scott Overby hammers home the fact, mistakes aren’t something you can fix later on, if you want to effectively prevent on-the-job incidents.
“As far as fall protection goes, you must be proactive. You cannot be reactive. If you're reactive, it’s too late. You may have injured somebody or someone may have not followed your guidelines and procedures and injured themselves.”
How HCSS Safety Helps Protect Workers
HCSS has spent years fine-tuning its construction safety management software, continuing to work on improvements every single day. For customers like McInnis Construction, the power of HCSS Safety shines within their ongoing work.
“Let me say, I don't know how people do it without HCSS Safety,” Overby says. “When you bring on new employees and you go through new employee orientation, HCSS shows up. There’s a place in there for you to record your training documents, and if you have a large group of say, 10 people that come in – and I’ve had at least that many or more – you can record the meeting right there and HCSS captures their signatures.”
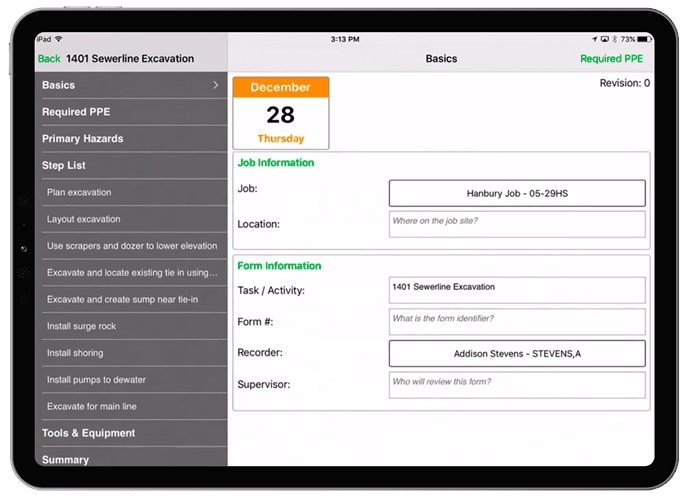
After hitting send, the meeting automatically goes into the skills and displays as a certification. As people consider HCSS as a safety tool, this step usually ends up being a big deciding factor.
“When an employee comes on board, we have his harness, we have his lanyard, and we make the assignment to him,” Overby continues. “I’m able to create my own inspection forms in HCSS where we record all the details.”
The scope of these details recorded is impressive, including who is the competent person inspecting, who the equipment is assigned to, and even making note of the serial number and date of service. Then when the employee puts the equipment on, you can take photos of him wearing that equipment properly, which is recorded right on the form. This not only proves the equipment was issued in good working condition, but in the event the employee leaves the company, you have a system for retaining that costly equipment so it can be returned.
“By the way, if you have an incident and OSHA comes on site, what's the first thing they’re going to ask for?” Overby adds. “They're going to want to see inspection reports and training records. You recorded all that in the very beginning, the first day on the job, when the worker came in for his new employee safety orientation. In the event of an incident, you’re able to recall all the training and inspections literally in seconds, but we'll say minutes to be conservative.”
Eliminate the Fear of OSHA Compliance
In general, there is often a feeling among construction companies about OSHA that they are not your friends, and you don't want their compliance officers on your jobsite doing walkthroughs where you can get cited and/or fined.
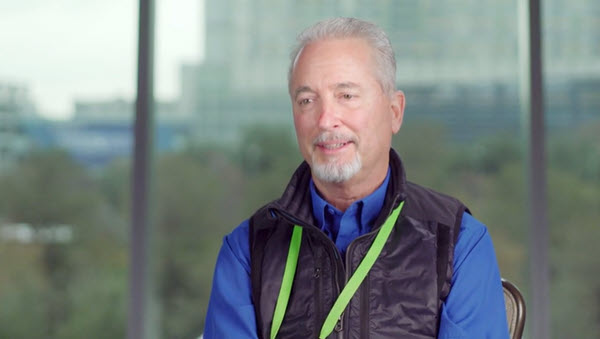
However, Overby is glad to tell you, based on extensive experience, that a company’s interaction with OSHA will only be negative if you aren’t crossing your t’s and dotting your i’s.
“Again, HCSS helps us to be successful in that area,” Overby says. “Yes, it’s expensive to have the right equipment to be compliant, but at McInnis, we want to be more than compliant. We want to engage our employees with best practices. Sometimes the training is a little bit more intensive, but the investment upfront far exceeds any citation that you could ever receive.”
Ready to Save More than Just Data?
HCSS has no interest in selling you something your operation doesn’t need. If your company wants to increase its fall protection program by implementing technology, HCSS might be the right fit for you.
Schedule an HCSS Safety demo to find out!