How to Successfully Improve Safety with Technology
“Most people in the construction industry don’t seem to be too open to change, but the way we rolled it out, it wasn’t completely overwhelming, and they’re really liking it.”
– Eric Waterkotte, Vice President - Safety, Millstone Weber
As the Vice President of Safety, Eric Waterkotte is a certified safety professional with nearly 20 years in construction safety. His company, Millstone Weber, is a heavy civil contractor specializing in mass transportation, with their bread and butter being heavy highway and bridge construction, as well as work for the Department of Defense.
Always available to help a customer is the Product Manager for HCSS Safety, Gen Simmons, who couldn’t be more passionate about imparting time-saving innovations and easy-to-understand reporting to industry professionals in need. During a recent webinar, the two sat down to discuss Millstone Weber’s journey of improving safety with technology.
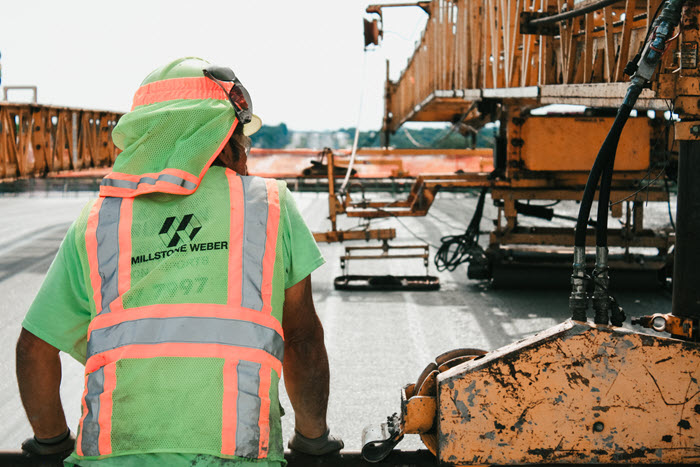
The Danger of Procrastinating on Getting Safety Software
After entering the construction industry in 2004, Eric Waterkotte immediately knew that everything safety-related needs to be documented. He put his own system in place where paperwork would eventually make its way back to the office, but put off implementing software, knowing at some point he was going to have to make the switch. Meanwhile, the company was growing into new states, and Waterkotte found his team juggling multiple projects covering an expansive radius.
“Most people don’t like change,” Waterkotte says, explaining why adjusting to technology took so long. “I’m one of those people, and it was just kind of overwhelming.”
For any teams out in the field who might fear this is just another annoying piece of admin work to do, Millstone Weber will attest the complete opposite is true: their teams actually cut down on the amount of time they have to spend paper-pushing, and foremen and superintendents appreciate that reduced amount of work.
“From an administration standpoint, it’s cleaned up the total amount of hours on my end,” Waterkotte says. “I’ve talked to our field people who are now doing their toolbox talks through this. After a few weeks of seeing them using it and reaching back out to get some feedback, a lot of them came back with comments like, ‘Man, this is saving me at least 10 minutes every morning kicking off my daily huddle!’ Again, most people in at least the construction industry don’t seem to be too open to change, but the way we rolled it out, it wasn’t completely overwhelming and they’re really liking it.”
If there is ever an accident in the field, companies have to track down the paperwork to prove whether or not they were at fault. With the wrong safety system, incident reports are not always easy to locate, which could mean major trouble. That lack of accessibility is downright dangerous for a company and can result in jobsites being shut down with loss of production time enforced. Worse, you might have the wrong employees working in situations they are not properly trained for, and that could result in severe accidents.
Fortunately, when using software like HCSS Safety, OSHA might make a site visit, and in just minutes, right there on the spot, your field employee can pull up all of the paperwork and photos needed.
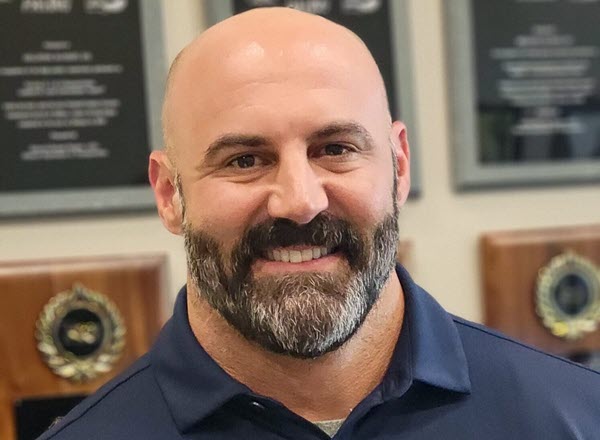
“I was tracking all of our employee training and certifications kind of by topic,” Waterkotte continues. “In total, I was probably keeping an eye on 20 to 30 different spreadsheets of people’s training. Well, with the [HCSS] system, once you have that information in there, it’s all self tracked. There’s a dashboard that shows me who is coming up for expiration. Those that are licensed with the software, all they’ve got to do is open up their iPad. They can search by skill or by employee with the attachments of their certs, all right there that they can pull up. There’s just a lot of steps that have been cut out now.”
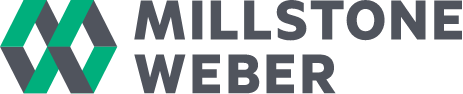
WHO:Millstone Weber, LLC
WHERE:St. Charles, MO
INDUSTRY:Heavy Civil Transporation
SOLUTIONS:Safety
OSHA estimates that contractors save $4-6 for every $1 invested in an effective safety program.
Source: OSHA
More Benefits of Technology
Another massive benefit of technology is assigning QR codes to workers that can be attached to any hard hat or badge. No one has to search, they simply scan the QR code and it immediately pulls up that worker’s skills and certs.
“That way you don’t even have to be a licensed user to check to see what training somebody has,” Waterkotte says. “You open your camera on your phone, scan their little sticker on their hard hat and boom, all their certs are right there, when they got it, when it expires.”
For safety managers out there who are still stuck on Excel, Gen Simmons has some advice. “You want a tool that lets your field team enter in your inspections, your JHAs, your meetings, so in the office, your safety professionals can just say, ‘Oh, I can see on this dashboard, I can see on this report, that we’re getting in our required compliance items,’ and allow you to see if there are any deficiencies. It’s just so much easier to manage risk and compliance when it’s easy to see.”
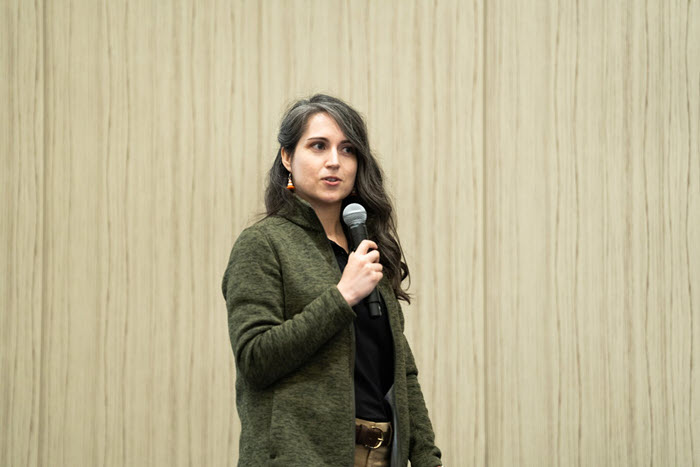
For Millstone Weber, getting this data doing the work for them is a massive benefit.
“All these inspections, when they’re sitting in a file cabinet, I couldn’t do much with that,” Waterkotte adds. “Once all those inspections are in the system, the system automatically creates analytics. You can break the data down now. [The software] identifies trends, identifies at-risk jobs by the types of incidents or near misses that the system is seeing. That’s been really good, having useful data now.”
How to Start Rolling Out Safety Software
Depending on the size of your company, it’s incredibly difficult to manage a strong safety program while a company is growing, especially as different jobsites start getting farther away from the home base where it’s easy to get everyone driving out there and checking on things.
“When I first started, all of our jobsites were probably within a 45 to 60-mile radius of the Greater St. Louis area,” Waterkotte recalls. “When the housing bust and economy dropped out, that’s when we started branching out. It was getting to be more difficult to manage these things like inspections and follow-ups and holding people accountable.”
Getting started with onboarding of the software help they needed, Waterkotte made sure to grab at least one superintendent from every department to ensure representation in all areas of their company. This resulted in 38 licensed users to start, whereas that number would have been closer to 70 or 80 if it had been all of them. Taking this route made it easier and more manageable to efficiently roll out their safety program of choice, HCSS Safety.
“Once we identified those 38 licensed users, we had a representative from HCSS come in on the training days where we brought out groups of 10 for two or three hours,” he says.
Buy-in from the field isn’t always easy to come by, but Eric Waterkotte has followed up with his crews multiple times to gather their thoughts on using safety software.
“I simply ask them, ‘Would you go back to doing things just on paper and pen?’ It’s all been positive. I’ve had nothing negative. The more you use it, the more familiar you are. After a week or two, if you’re using it each day, it’s pretty basic. I mean, it was designed for a field foreman to use, not overcomplicating it. The one thing I regret on my end with this is that I didn’t do it years ago.”
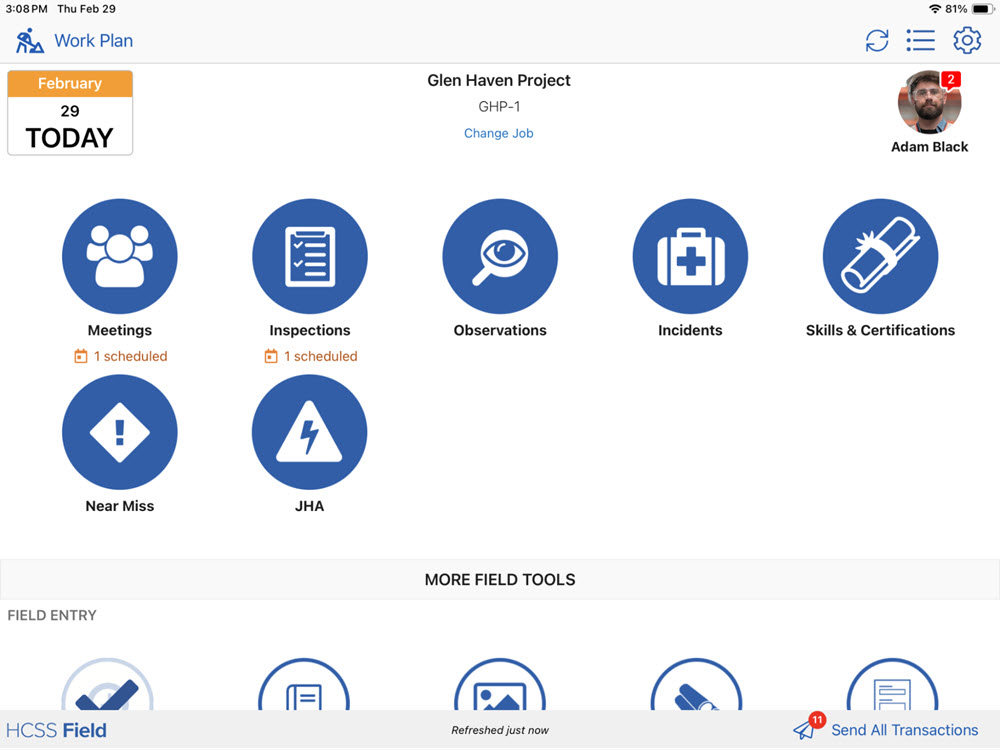
Top Things to Look for in Software to Help Support Your Team
When safety professionals are searching for software programs to decide what tool works best for them, it can be tough determining what exactly to watch out for. For Eric Waterkotte, the answer isn’t as complex as you might think.
“Just simplicity of the system and the way it’s set up, simple for a field foreman to be able to use,” he answers. “Ask yourself, ‘Am I efficient with how I’m doing things?’ I thought I was because I’m a pretty organized person, but I was very inefficient [in] how we were managing a lot of this stuff. Look at your culture, look at your accountability. If you think your accountability’s lacking, this can only help.”
Since it’s always a challenge to get started with something new and realize the administrative commitment involved, Gen Simmons recommends bringing in other people within your company to have those initial discussions about the software with somewhere around 10-15 questions and concerns prepared.
“Anyone that has questions for me on just safety software in general or HCSS Safety, [I’m] happy to talk through what some of the pitfalls can be so you know what to look out for,” she says.
Ready to get more info? Request safety software information from HCSS, and a technology expert will gladly discuss solutions that might help!
Grow your business with HCSS
Fill out the form to see how our software solutions can help you throughout each stage of the project lifecycle