J.F. Brennan Company, Inc. (Brennan) is a fourth-generation, family-owned marine construction firm specializing in environmental remediation, dam construction, commercial diving, harbor management, and submarine cable services. Since 1919, Brennan has worked closely with public and private owners of water-based infrastructure and operates nationwide throughout coastal and inland waterways.
Overcoming Regulatory Challenges
Considering Brennan’s extensive range of services, they must collaborate with numerous regulatory authorities, including the Environmental Protection Agency (EPA), the Occupational Safety and Health Administration (OSHA), the Mine Safety and Health Administration (MSHA), and the United States Army Corps of Engineers. Plus, they need to monitor their safety and quality across dozens of jobsites at a time.
“The biggest obstacle we face is that we are so spread out,” says Steven Skau, Vice President – Safety. “We have so many crews across the country, and over 600 employees. So, we might have crews working in 30 to 40 different locations at one time.”
Brennan adopted HCSS Safety to help collect data to confirm adherence to all those environmental and safety regulations and to gather all data from so jobsites in one place. HCSS Safety was just what the company needed to sort through and make sense of all the safety data it collects.
"The ability to record and submit our safety-based observations on phones and iPads really changed things. It’s a huge upgrade. It’s cut down a lot of time in our Safety department and frees up time for our crews in the field, all while increasing the quality of those submittals."
– Steven Skau, Vice President of Safety
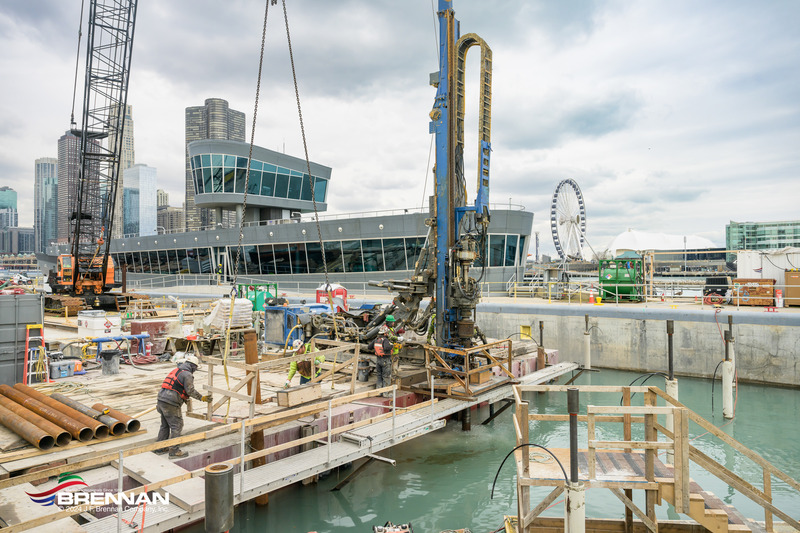
Engaging Employees
Fortunately for Brennan, their safety program has always prioritized getting field employees involved. The company has weekly, company-wide safety meetings every Monday morning to discuss safety-based observations the safety department has received. Everyone, from those on jobsites to the organization’s CEO, all call into the meeting.
“The fact that we can tie all of our data and reports together and talk about it weekly or even daily is really huge,” Skau says. “That capability is really important to us. It’s the one thing that really ties all our divisions together.”
The company accepts safety-based field observations that are submitted by employees from jobsites and work areas, which it then distributes to the whole company to discuss. In the past, getting these submissions on paper, often days or weeks after the observation occurred, left little time to address important issues as they were happening.
“The ability to record and submit our safety-based observations on phones and iPads really changed things. It’s a huge upgrade,” Skau comments. “It’s cut down a lot of time in our Safety department and frees up time for our crews in the field, all while increasing the quality of those submittals.”
The Results of HCSS Safety
Before HCSS Safety, Skau mentioned that employees would make submittals on paper, either retyping them later in an email or turning them in at the end of a week or months later at the end of a project.
“The quality of our safety-based observations and submittals has gone up,” Skau says. “People are much more likely to take photos and send notes along at the time of the observation, rather than later.”
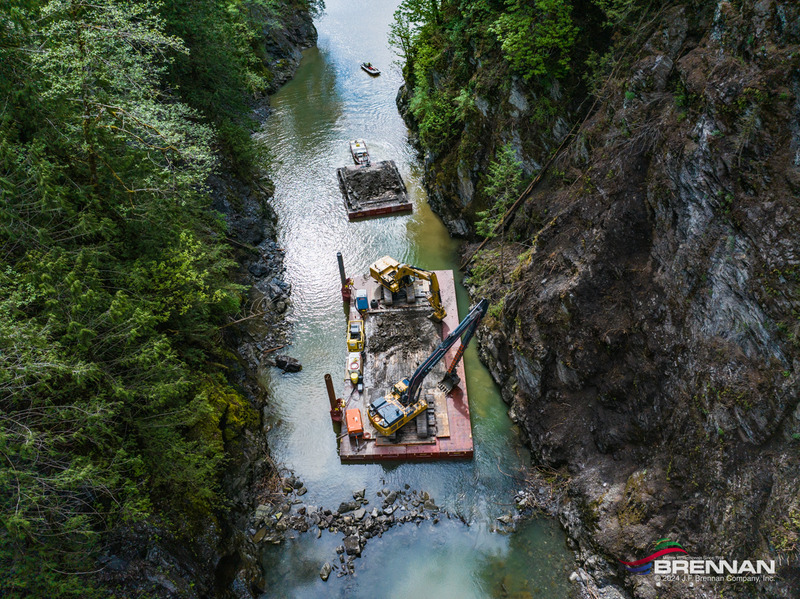
On top of communicating faster, the entire implementation of HCSS Safety and mobile devices in the field went relatively smooth for Brennan.
“When we went to the iPad system, there was a little resistance at first because it was new and unfamiliar,” Skau recalls. “But once they realized how easy it was to access and use the information, it freed up time for our teams.”
Achieving a Lower EMR
In their first 5 years using HCSS Safety, Brennan lowered their Experience Modification Rate (EMR) – the number insurance companies use to gauge both past cost of injuries and future chances of risk and assign worker’s compensation insurance premiums to companies – to a .61. Years later, that number is even lower at .58. That low number means less indirect costs to Brennan when bidding on jobs, allowing them to bid work at a lower cost.
“The safety observations are a key part of that because they are critical to what we were doing before,” Skau adds. “The most critical part, to us, is having everything centrally located and tying it all together.”
Receiving safety observations immediately, as they are captured and as the observed event is occurring, is important to be able to address issues in a timely fashion. It also allows their workers to retrieve historical information quickly and easily.
For a job that is only a month long, capturing an observation on the first day and being able to address it in the global meeting that same week can help prevent an accident from occurring.
“It allows us to look at the leading indicators that the industry is really pushing now,” Skau continues. “Rather than gathering information after the fact and trying to hindsight things, all that information is there in real-time for us to use. We can classify it and use our time to get some leading indicators rather than using that time just to gather information.”
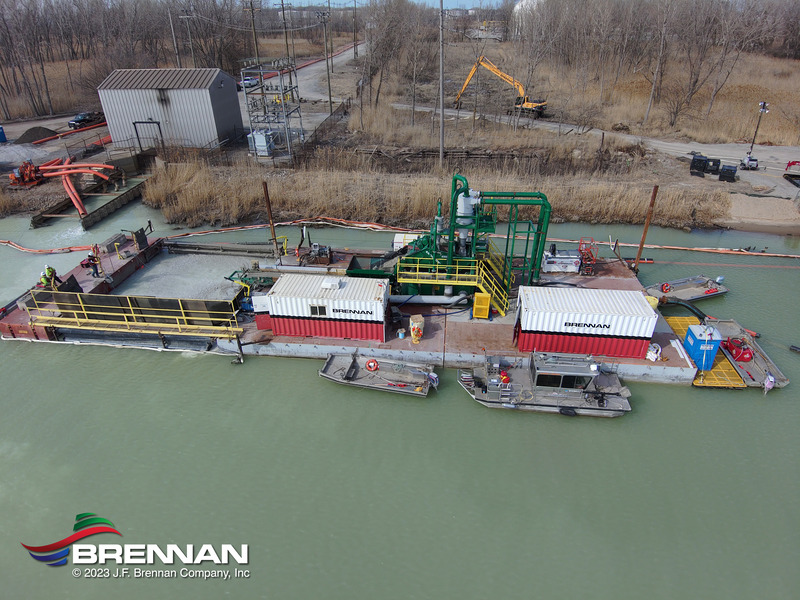
Maximizing Their Use of HCSS Safety
Because the company does so many different kinds of marine work, there is an abundance of certifications and skills that require tracking and maintaining.
“We do a lot of in-house training and a lot of external training,” says Daniel Palen, Vice President – Marine Safety & Compliance. “It’s huge for us to be able to click on a class or type in ‘confined space’ and go right to it, and for us to have the alerts to everybody coming due so we can notify them, rather than going through old paper files and multiple spreadsheets.”
The company also places high value into its toolbox talks, including ones that focus on the specific work Brennan does, like diving and dredging regulations and inspections.
“The daily toolbox meetings have become more of a work agenda for the day,” Palen says. “We don’t just pick a topic randomly and discuss it. Our foremen and superintendents are awesome – they say, ‘Here’s what we’ve identified as the hazards of the day because of the work you’re doing.'”
Add HCSS Safety to Your Operations
HCSS Safety® is a complete safety system with a web application, mobile app for tablets and smartphones, and more than 1,000 pre-built meeting, inspection, and JHA templates, allowing you to quickly build a comprehensive safety program that is simple to manage in the field or office.
To start your world-class safety program using HCSS Safety, reach out to one of our software experts today for a custom demo!
“It’s huge for us to be able to click on a class or type in ‘confined space’ and go right to it, and for us to have the alerts to everybody coming due so we can notify them, rather than going through old paper files and multiple spreadsheets.”
– Daniel Palen, Vice President - Marine Safety & Compliance